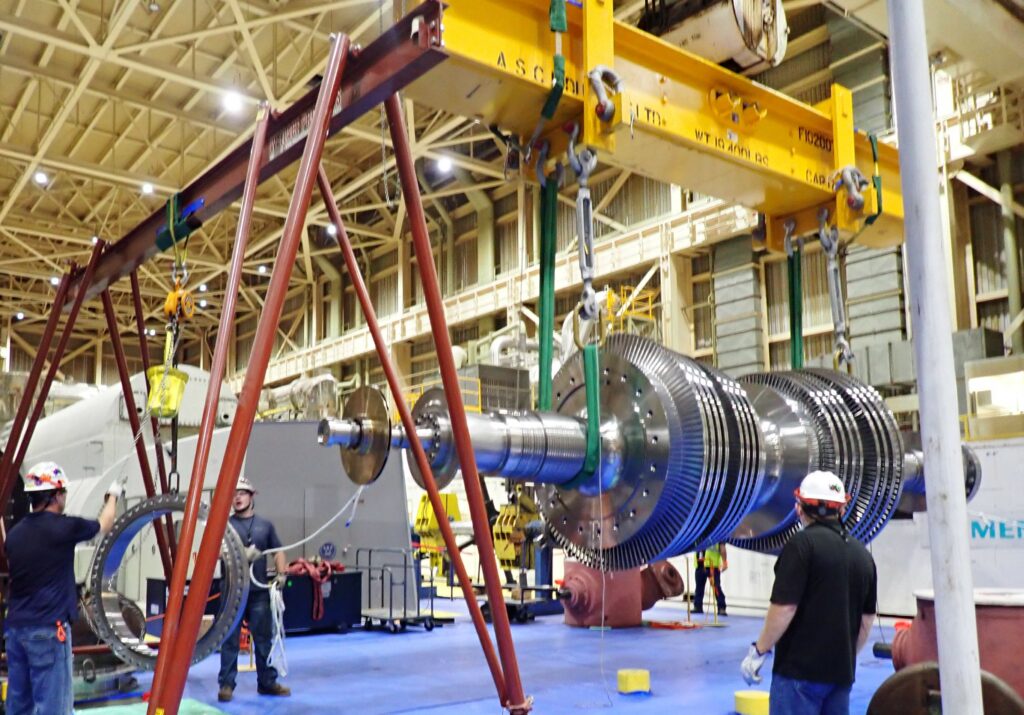
Using a new technique called “virtual alignment,” Siemens Generation Services and Southern States Millwrights replaced 40-year-old machinery during a spring 2021 upgrade of Unit 1 at Farley Nuclear Station near Dothan, Alabama. The team completed the project, which increased the plant’s output by more than 26 megawatts and improved its reliability, 100 hours ahead of schedule.
The overhaul included: installing a new high-pressure rotor, guide blade carriers, and blade rings; retrofitting a steam generator feed pump with new components; and replacing several valves.
“Reducing duration by four days – that’s massive,” said Jason Guggisberg, district service manager for Siemens. “That’s a significant amount of revenue for Plant Farley and for Siemens. And it’s a direct result of feedback from craft and implementation of lessons learned.”
In fall of 2020, Siemens Generation Services and millwrights from Southern States Millwright Regional Council upgraded Unit 2 of Alabama Power’s dual-unit Plant Farley. Millwrights cataloged “lessons learned” from the Unit 2 project, and the team drew on this knowledge during the Unit 1 project.
Adaptations
“A lot of issues we faced with the fall outage were anticipated and dealt with preemptively with the spring outage,” said Shane Harris, millwright craft labor supervisor.
Sarah Wilson, a journeyman member of Millwright Local 1263 who worked on both the fall and spring outages, said there was a learning curve with the rigging involved in removing old equipment. In order for the new components to fit properly, a lot of machining activities had to take place in the lower half of the cylinder, Harris said, and some of the hole alignments were off during the fall project. All these challenges and solutions were recorded.
“We saw what could be expected for the other unit,” Wilson said.
With the support of SGS, that made the second project go smoother and faster. “This time, as soon as a component came in, we verified it and performed the machining,” Harris said.
While conducting their routine inspection of parts and components, millwrights identified a five-foot-tall stud that needed to be replaced due to cracks and bad threads, Wilson said. “It was one of the studs that holds the entire shell together,” she said. “When you set the hood down, the guide bolts and the studs make sure the entire shell sits in place correctly and the hood goes back on safely.”
Virtual alignment
A new computer-modelling method also helped reduce outage duration and customer risks. “We make 3D scans of our parts, assemble them in virtual space, and then decide the machining that’s required to assemble a machine one time versus putting it together and taking it apart several times,” Guggisberg said. “It’s really cool.”
SGS used the same technique with the fall outage and improved it in the spring based on feedback from millwrights and other craftspeople. “We were able to enhance the process, and, as a result, our performance during the outage,” Guggisberg said.
Jobsite culture
The fact that SGS and its customer Southern Nuclear listened to and implemented millwrights’ suggestions added to an extremely positive jobsite atmosphere, said Anna Rademakers, manager of nuclear service for SGS. “When the contractor and the customer treat the craft like they’re important and part of the team and contributing, it makes a huge difference,” she said.
Guggisberg said the millwrights took their top-notch performance to an even higher level with the Unit 1 project. “It was one of the best outages I’ve ever been a part of,” he said. “There is a culture that they brought to the deck. Everyone was working hard, everyone left tired and dirty, but everyone was having a good time.”
In a Plant Farley customer-satisfaction survey, SGS earned a five out of five for on-site performance during the Unit 1 project. “That’s not because we had the best plan,” Guggisberg said. “It’s not because we had the best management. It’s because we had an awesome team. It directly reflects on craft and the millwrights in particular.”
Harris said the millwright team came together and worked as one. “We had a lot of fun and did a lot of great work in a very short amount of time,” he said.
Customer accommodations
To help protect craftspeople from COVID-19 and prevent them from having to go through security multiple times per day, Southern Nuclear provided free breakfasts and lunches for the duration of the project, which began in January and ended in April.
“They have a cafeteria, but it’s outside a protected area so there are a lot of touch points,” Rademakers said. “If people need to leave the turbine building and go through security and go into the support building and then enter the cafeteria, imagine all the door handles and everything that people have to touch and all the interfaces. That was definitely a nice gesture.”
Logistics and manpower
The SGS team was comprised of 90 craftspeople, including 47 millwrights as well as pipe fitters, laborers, boiler makers, operating engineers, and two carpenters.
Rademakers said working with David Bonds, nuclear representative for the SSMRC, to fill the millwright positions was “seamless.” Because the SSMRC has one point person for nuclear projects, she does not have to coordinate efforts with multiple business agents.
“David knows what we need and who we need,” she said. “We get all the information as far as the scope and the manpower counts, and it’s basically a well-oiled team. We also do the background screening for the Plant Farley site, so we have a very streamlined process. No one is sitting around being unproductive. When folks come in, they’re doing their training, they’re getting badged, and they’re on the deck.”
Relationship history
Rademakers said the SGS-SSMRC relationship has been exceptional since the SSMRC was formed in 2010. “The reason why it’s excellent is because we act as a team,” she said. “When things are going good, great. And if anything’s not going right we look at what modifications need to take place, and we execute them right away.”
SGS and the SSMRC must have the same goals and objectives to be successful, Guggisberg said. “The millwrights make or break our project, and I have a high degree of confidence in them,” he said.
Rademakers said long-term contracts are just a ticket to get on the bus. “If you don’t do well at any outage, you could be thrown off the bus,” she said.
SGS has worked at Plant Farley since the 1970s, with only a brief break in the 2000s.
Harris said SSMRC members like to work with SGS because safety is the company’s No. 1 priority. Wilson backs that up. “I like their safety aspect,” she said. “They want to make you feel safe, like a team, a family,” she said.
When safety is prioritized, high productivity and quality follow, Harris said. “If we get it done safe, don’t have any injuries or incidents, then nine out of 10 times the schedule and everything else will fall into place,” he said. “And they believe that.”
Upcoming work
Guggisberg said SGS has significant work planned at Plant Farley through 2026. “It is so strategically important that this outage went well,” he said. “It ensures all of our futures at Farley.”
Upcoming work includes low-pressure turbine inspections in spring of 2022, spring of 2024, and spring of 2025. Generator stater rewinds, which will shut down the plant for 60 days, are scheduled for the fall of 2022 and the fall of 2023. Valve work, auxiliary work, and more are slated as well. “A lot of maintenance is coming up, and millwrights are key to our success,” Guggisberg said.